7 Factors That Affect A Magnets Performance

All magnets have a 'pull' rating measured in kilograms and this relates to how much force acting perpendicular to the magnet is required to pull the magnet from a steel plate or equal thickness when in direct, flush contact.
The 'pull' rating is obtained under the following ideal conditions:
- The test bed steel plate is thick enough to absorb all the magnetism (typically 10mm thick)
- It is clean and ground perfectly flat
- The pulling force is slowly and steadily increased and is absolutely perpendicular to the magnet face.
In real-world applications, perfect conditions are unlikely, and the below factors will affect the magnet and reduce the performance and given pull of the magnet:
STEEL THICKNESS
Absorption of magnetism
The thickness of a steel surface a magnet is attracting to can impact the performance and pull of a magnet.
If a magnet requires the contact steel to be 10mm thick in order to absorb all the magnetism and ensure for maximum performance and pull, then applying the magnet to a 1mm thick steel surface will result in the magnet losing 90% of its magnetism and therefore only delivering 10% of its maximum capability.
It is therefore important to ensure that a magnet is attracting to the surface with its full performance and no stray magnetism is leaving the steel.
A way to test and ensure no magnetism is lost is by fixing the magnet in place on the steel surface, and then applying a small steel plate behind the contact steel. If the small plate remains attracted behind the contact steel, then the magnetism is not being fully absorbed by the contact steel which indicates that the thickness of the steel is insufficient.
Alternatively, if the small steel plate falls away from behind the contact steel, then the steel is fully absorbing all magnetism, ensuring the magnet is providing its maximum pull and performance. Applying thicker steel will not increase the pull of the magnet.
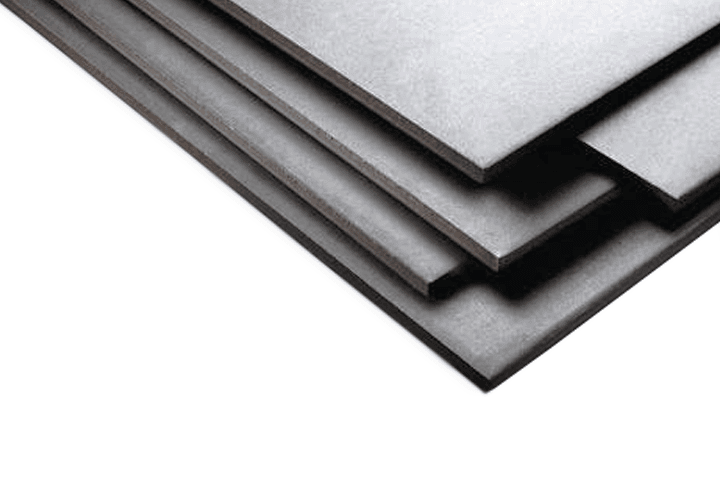

AIR GAPS
Affect magnetic circuit
Another factor that will reduce the performance and pull of a magnet is if there is presence of any air gaps. An air gap refers to any non-magnetic material that prevent magnetism from attracting to another magnet or ferrous object.
Air gaps can occur if the contact steel is rusty, dirty, painted or uneven for any reason, which will cause a loss in magnetism.
As a magnet produces a magnetic circuit, any air gap will cause a break in this and subsequently means that magnetism has to ‘jump’ from the magnet to the other magnet or ferrous object to continue the circuit.
The bigger the air gap, the bigger the reduction in the magnets pull and performance. If you would like to find out more information on the ‘Pull-gap’ curve which describes how pull strength decreases as the size of an air gap, view the term within our Magnet Glossary.
MATERIAL
Determines ability to conduct magnetism
The material in which the magnet is attracting to will affect its performance. When magnets are tested to identify their pull strength, a mild steel is used as the contact steel.
Mild steel is preferred to alloy steels and cast irons is the ability to conduct magnetism is far higher.
Alloy steels and cast irons have a reduced ability to conduct magnetism which therefore reduces the pull of a magnet and it will not perform at its maximum capability.
Cast iron in particular can reduce the pull of a magnet by as much as 40% due to the fact that cast iron is much less permeable than mild steel.
Materials such as Copper and Zinc are not magnetic, and as such are commonly used as coatings for magnets.
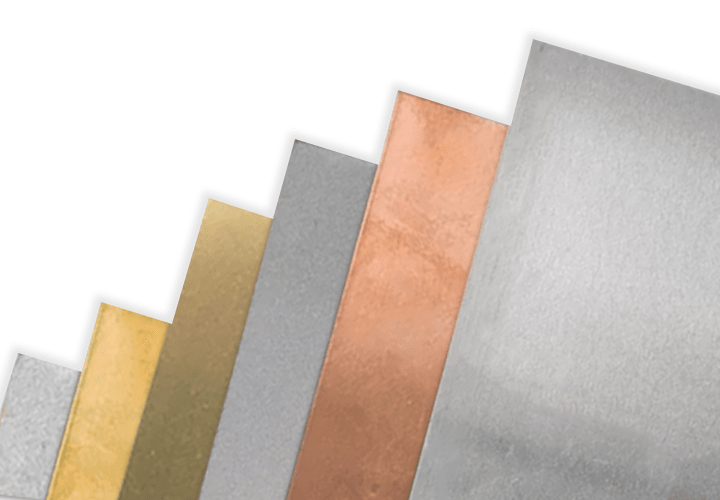
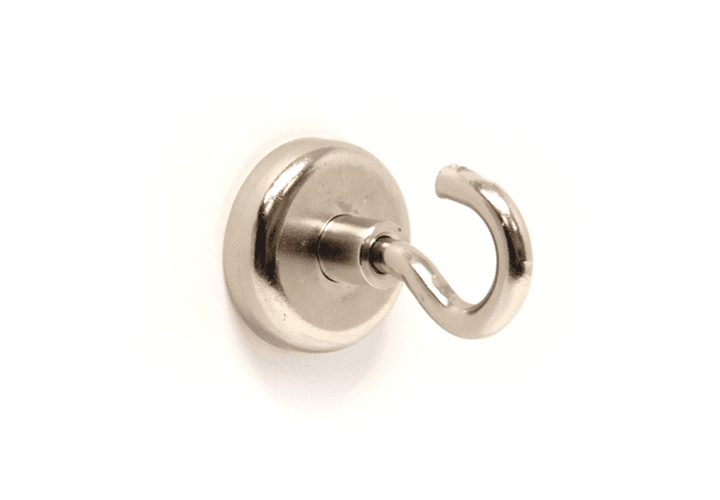
SHEER FORCE
Determines performance
Sheer force is another factor that affects the performance and pull of magnets. Magnets can be fixed within a sheer or vertical position which is dependant on the application. When magnets are fixed in a vertical position, this is known as the sheer position.
It is five times easier to slide a magnet than to pull it away from the surface it is attracting to. This is due to the coefficient of friction which is typically 0.2 for steel on steel surfaces.
If you were to apply a magnet to a steel surface that has a pull strength of 10kg in a sheer (vertical) position, the magnet will only support 2kg - this should be considered when looking to use a magnet in a sheer position, and the weight of the item being loaded on to the magnet must be considered when assessing the pull strength required from the magnet.
If the load is heavier than the magnets sheer position pull, the magnet will begin to slide down the steel surface.
TEMPERATURE
Maximum operating temperature
Subjecting a magnet to temperatures above its maximum operating temperature will cause it to lose performance, which won’t be recovered on cooling.
Repeatedly heating beyond the maximum operating temperature will result in a significant decrease in performance.
This is due to the magnetic domains within the magnet becoming miss-aligned, which will in turn cause the magnet to lose its magnetism.
In contrast to this, when a magnet is continuously exposed to low temperatures, the strength increases due to its magnetic properties being enhanced.
The table (right) identifies magnetic materials and their respective maximum operating temperatures.
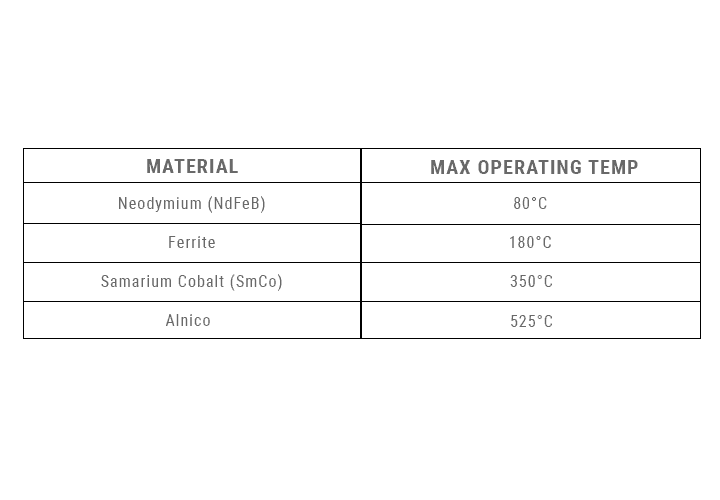
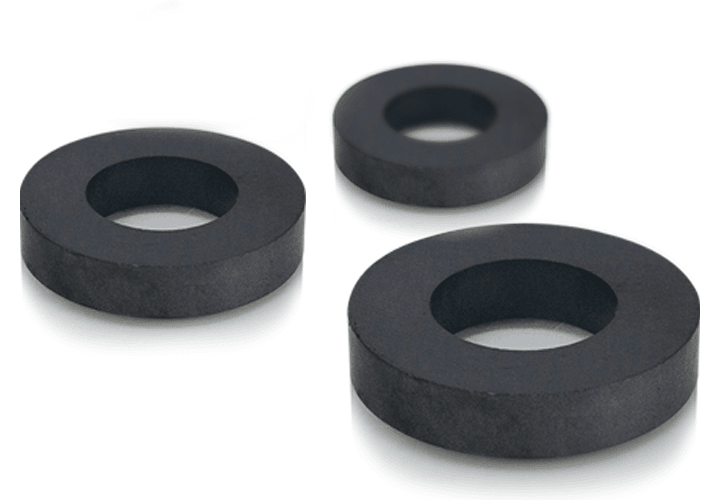
HEAT
Exceeding maximum operating temperature
As mentioned within the temperature section, a magnets performance and pull will be reduced with continuous exposure to high temperatures.
Exceeding the maximum operating temperature (e.g. 80°C for N42 Grade Neodymium Magnets), will miss-align the magnetic domains within the magnet and magnetism will be lost.
If magnets are continuously exposed to heat above their maximum operating temperature, they will become permanently demagnetised.
Magnets such as Samarium Cobalt, Ferrite (pictured left) and Alnico are designed to maintain performance under extreme heats and as such are commonly used within high temperature applications. You can find our wide range of high temperature magnets here.
CORROSION
Exposure to water
Many magnets are used within outdoor applications, where it is common for harsh weather conditions to exist. Exposure to water can affect the performance and pull of a magnet.
If the plating on a magnet becomes damaged, the magnet can become exposed to water. This exposure to water can cause the magnet to rust, resulting in a deterioration in the magnetic performance.
There are many magnets that are therefore designed to maintain performance under these harsh conditions.
Samarium Cobalt and Ferrite magnets are both resistant to corrosion, but are not as strong as Neodymium magnets. If you are looking for corrosion resistant magnets, take a look at our extensive range here.
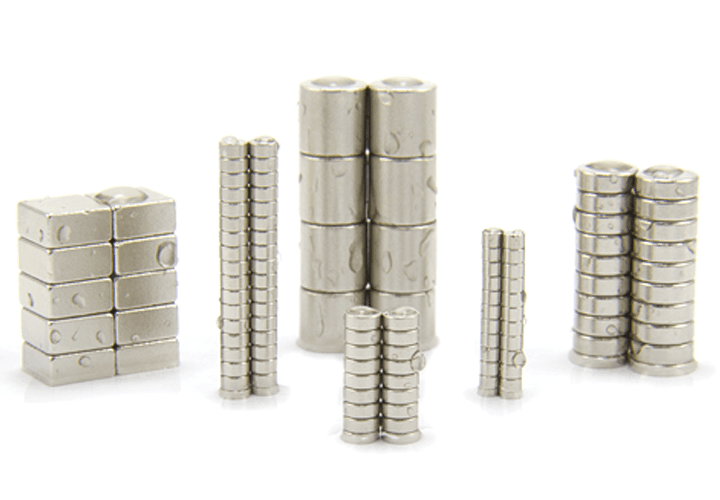